I have just tonight realised that to correctly do the drill/tap operation on each of these slugs I need a V block to hold it square in both axes in the vice.
May try to in-press grind the top of them flat, though. But not tonight. Should probably do that with a V block, too, but meh, can redo if I make it worse.
Currently both blocks have one bad end off by a few degrees and one okay end that is domed from my attempt to square it by rotating it against the cut off wheel in the chop saw.
So all they really need is a light touch in the middle to bring that down and leave the outer edges as is, flat relative to each other.
Mobile vice and small anvil / welding table
Re: Mobile vice and small anvil / welding table
DIYEFI.org - where Open Source means Open Source, and Free means Freedom
FreeEMS.org - the open source engine management system
FreeEMS dev diary and its comments thread and my turbo truck!
n00bs, do NOT PM or email tech questions! Use the forum!
The ever growing list of FreeEMS success stories!
FreeEMS.org - the open source engine management system
FreeEMS dev diary and its comments thread and my turbo truck!
n00bs, do NOT PM or email tech questions! Use the forum!
The ever growing list of FreeEMS success stories!
Re: Mobile vice and small anvil / welding table
Discovered these things yesterday evening, too: https://twitter.com/FredCookeNZ/status/ ... 5379666944

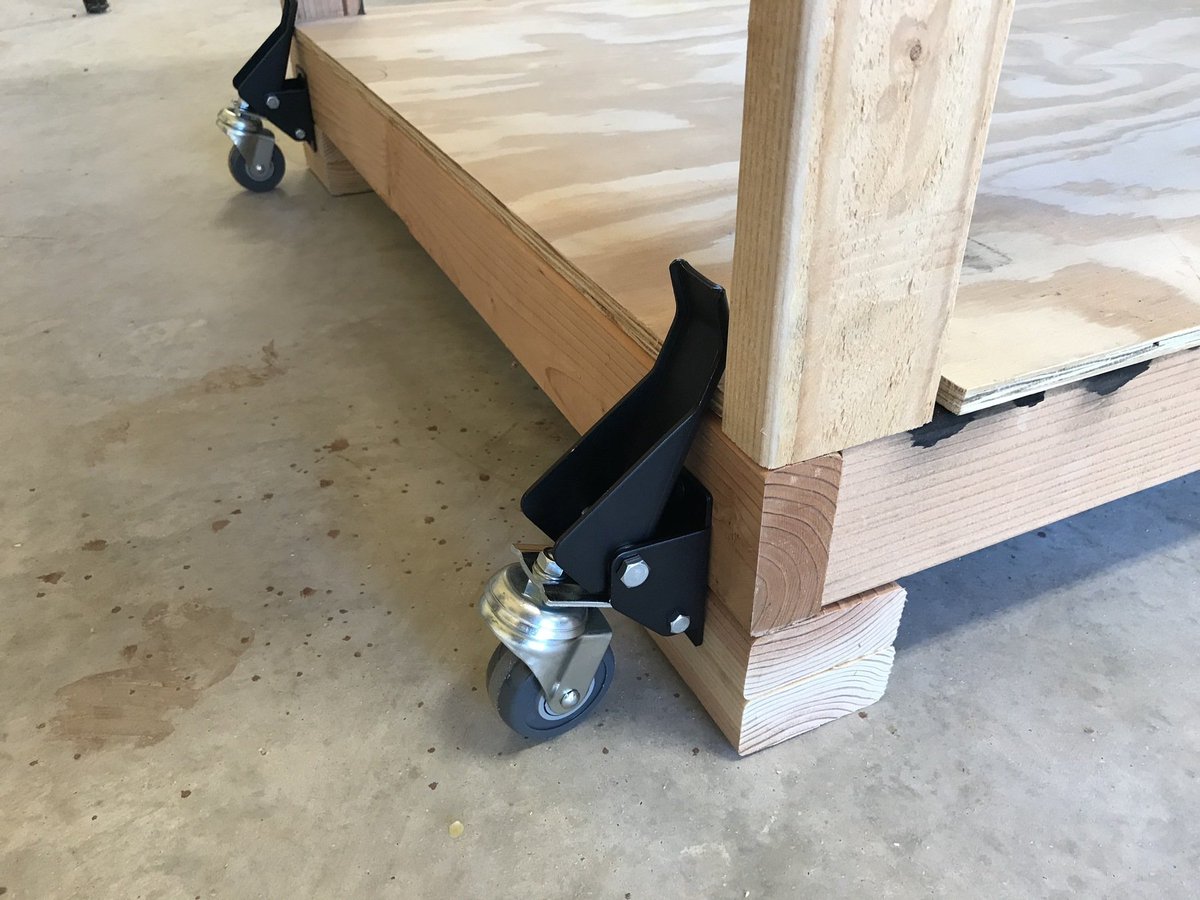

Link: https://www.rockler.com/rockler-workben ... kit-4-pack
Also, DIY surface grinder is excellent, but dangerous in current form. Need to upgrade the setup for a better grip in the chuck, or maybe a MT4 arse end. However I ground the ends of those slugs flat and square no worries :-D More later.
Link: https://www.rockler.com/rockler-workben ... kit-4-pack
Also, DIY surface grinder is excellent, but dangerous in current form. Need to upgrade the setup for a better grip in the chuck, or maybe a MT4 arse end. However I ground the ends of those slugs flat and square no worries :-D More later.
DIYEFI.org - where Open Source means Open Source, and Free means Freedom
FreeEMS.org - the open source engine management system
FreeEMS dev diary and its comments thread and my turbo truck!
n00bs, do NOT PM or email tech questions! Use the forum!
The ever growing list of FreeEMS success stories!
FreeEMS.org - the open source engine management system
FreeEMS dev diary and its comments thread and my turbo truck!
n00bs, do NOT PM or email tech questions! Use the forum!
The ever growing list of FreeEMS success stories!
Re: Mobile vice and small anvil / welding table
Chuck accepts > 45mm of M14 before it runs out of depth and there's only a mere 15mm hanging out past the nut on the current setup. So += 30mm if the nut is the same thickness means 80mm thread, thread all the way to the end - they may not make these? We'll see when I get to the bolt shop and ask the man. The thread is actually 5/8"-11 TPI UNC, not M14, that just happens to fit super dodgy.
With one slug tapped I can also say that I want the top fastener to be at least 65mm thread below the head, and the lower one that + 5-10, more the merrier and both can have up to say 15mm of non-thread if required, unlike the dodgy surface grinding setup above.
And I need a replacement 50mm long M14 cap screw to replace the one I've chowdered using it with too little hanging out in a dodgy china chuck.
So that's at least 4 bolts in 3 sizes, some washers, and one nut to buy:
cap screws unless nut/washer:
2 x M14x2 @ 50
1 x M14x2 @ 65+, 60 and 70 are options, can accept up to 18mm of non-thread shoulder absolute max, may require re drill to 15 or 16, no big deal.
1 x M14x2 @ 70, 75, 80, or 90 with up to 19mm of non-thread shoulder absolute max, ditto re redrilling
4 x hardened washers to suit
1 x 5/8-11 UNC @ about 80mm shank, but all thread, the most I can get with all thread, consider tapping to get full depth
2 x 5/8-11 UNC nuts each of several types, cut down to get more thread in chuck if need be depending on above
With one slug tapped I can also say that I want the top fastener to be at least 65mm thread below the head, and the lower one that + 5-10, more the merrier and both can have up to say 15mm of non-thread if required, unlike the dodgy surface grinding setup above.
And I need a replacement 50mm long M14 cap screw to replace the one I've chowdered using it with too little hanging out in a dodgy china chuck.
So that's at least 4 bolts in 3 sizes, some washers, and one nut to buy:
cap screws unless nut/washer:
2 x M14x2 @ 50
1 x M14x2 @ 65+, 60 and 70 are options, can accept up to 18mm of non-thread shoulder absolute max, may require re drill to 15 or 16, no big deal.
1 x M14x2 @ 70, 75, 80, or 90 with up to 19mm of non-thread shoulder absolute max, ditto re redrilling
4 x hardened washers to suit
1 x 5/8-11 UNC @ about 80mm shank, but all thread, the most I can get with all thread, consider tapping to get full depth
2 x 5/8-11 UNC nuts each of several types, cut down to get more thread in chuck if need be depending on above
DIYEFI.org - where Open Source means Open Source, and Free means Freedom
FreeEMS.org - the open source engine management system
FreeEMS dev diary and its comments thread and my turbo truck!
n00bs, do NOT PM or email tech questions! Use the forum!
The ever growing list of FreeEMS success stories!
FreeEMS.org - the open source engine management system
FreeEMS dev diary and its comments thread and my turbo truck!
n00bs, do NOT PM or email tech questions! Use the forum!
The ever growing list of FreeEMS success stories!
Re: Mobile vice and small anvil / welding table
Measured up the tension rod vs main tube sizes, and:
46 + 11 + extension + clearance - cut off = distance from end of tube.
Extension on the end I already pressed is a taper from 4-5mm and back again due to non-square cut in the tension rod tube. I'd probably go 5-6 on the other end for a bit more clearance while welding.
Clearance from washer to face should be big enough to not contact and small enough to not mean a longer/more expensive cap screw than necessary. 5mm ought to be enough for that.
So 57 + 10 is 67 with nothing cut off the tube. And given an ID of 128.2 that's still weldable. Plus plug welds. Maybe reduce the tube by 3mm to make it a 1:2 proposition? Otherwise leave it alone and get stuck in.
46 + 11 + extension + clearance - cut off = distance from end of tube.
Extension on the end I already pressed is a taper from 4-5mm and back again due to non-square cut in the tension rod tube. I'd probably go 5-6 on the other end for a bit more clearance while welding.
Clearance from washer to face should be big enough to not contact and small enough to not mean a longer/more expensive cap screw than necessary. 5mm ought to be enough for that.
So 57 + 10 is 67 with nothing cut off the tube. And given an ID of 128.2 that's still weldable. Plus plug welds. Maybe reduce the tube by 3mm to make it a 1:2 proposition? Otherwise leave it alone and get stuck in.
DIYEFI.org - where Open Source means Open Source, and Free means Freedom
FreeEMS.org - the open source engine management system
FreeEMS dev diary and its comments thread and my turbo truck!
n00bs, do NOT PM or email tech questions! Use the forum!
The ever growing list of FreeEMS success stories!
FreeEMS.org - the open source engine management system
FreeEMS dev diary and its comments thread and my turbo truck!
n00bs, do NOT PM or email tech questions! Use the forum!
The ever growing list of FreeEMS success stories!
Re: Mobile vice and small anvil / welding table
Very behind on progress updates in this thread, so here's a jump forward in time to a fully finished pillar section incorporating a ~10mm press/interference fit and a M14 based tension system. This thing is now ONE piece! :-D https://twitter.com/FredCookeNZ/status/ ... 3291548672

And tonight I selected the best of the three disks for the top, marked it top and bottom, rolled it over, transfer punched the flange pattern on, punched those to deepen them with the Starrett 18C 3 times each, and dragged it up onto the drill press table ready to pilot drill and prepare for tapping at 8.5mm for M10 threads. Tomorrow for that! :-)
And tonight I selected the best of the three disks for the top, marked it top and bottom, rolled it over, transfer punched the flange pattern on, punched those to deepen them with the Starrett 18C 3 times each, and dragged it up onto the drill press table ready to pilot drill and prepare for tapping at 8.5mm for M10 threads. Tomorrow for that! :-)
DIYEFI.org - where Open Source means Open Source, and Free means Freedom
FreeEMS.org - the open source engine management system
FreeEMS dev diary and its comments thread and my turbo truck!
n00bs, do NOT PM or email tech questions! Use the forum!
The ever growing list of FreeEMS success stories!
FreeEMS.org - the open source engine management system
FreeEMS dev diary and its comments thread and my turbo truck!
n00bs, do NOT PM or email tech questions! Use the forum!
The ever growing list of FreeEMS success stories!
Re: Mobile vice and small anvil / welding table
Very nice, that is one sturdy vice stand
So did you weld something to the inside for the M14 "tension system"?
(that has a really sophisticated ring to it)


Re: Mobile vice and small anvil / welding table
Yeah, I did, the 16mm thick fitted 128mm disk cut from the same piece as the flange pictured here. Disk seen on the previous page in this thread :-)
3 good deep quality plug welds and a shitty no-glove arm-inside-tube weld around the perimeter from only the top side. I intended to do a better one around the other side, but now that it's pressed together... no. :-D
Strong enough, if not pretty. I could add 3 more plug welds and then guarantee it'd be overkill strong, but I already tightened the fastener as much as I physically could and didn't come close to breaking what's already there.
Additional plan, going to splurge on 22kg of lead shot for duck shooting and fill the tube with it instead of sand. Will add stability, push the overall weight just past 200kg, and deaden any ringing from impacts. I hope.
Disk is drilled 40mm deep in matching pattern (3.5mm then 8.5mm) and M10x1.5 tap set ordered from a German company (Volkel with funny o) but probably not made in Germany sadly. Sold me on three stage taps that aren't just taper varied, but are actually partial cuts so the final bottoming tap actually takes a fine cut of its own all the way through. Will see how that works out relative to the conventional Sutton Aussie ones I intended to buy.
A couple of lame updates:
Yesterday or the day before: https://twitter.com/FredCookeNZ/status/ ... 4512784384
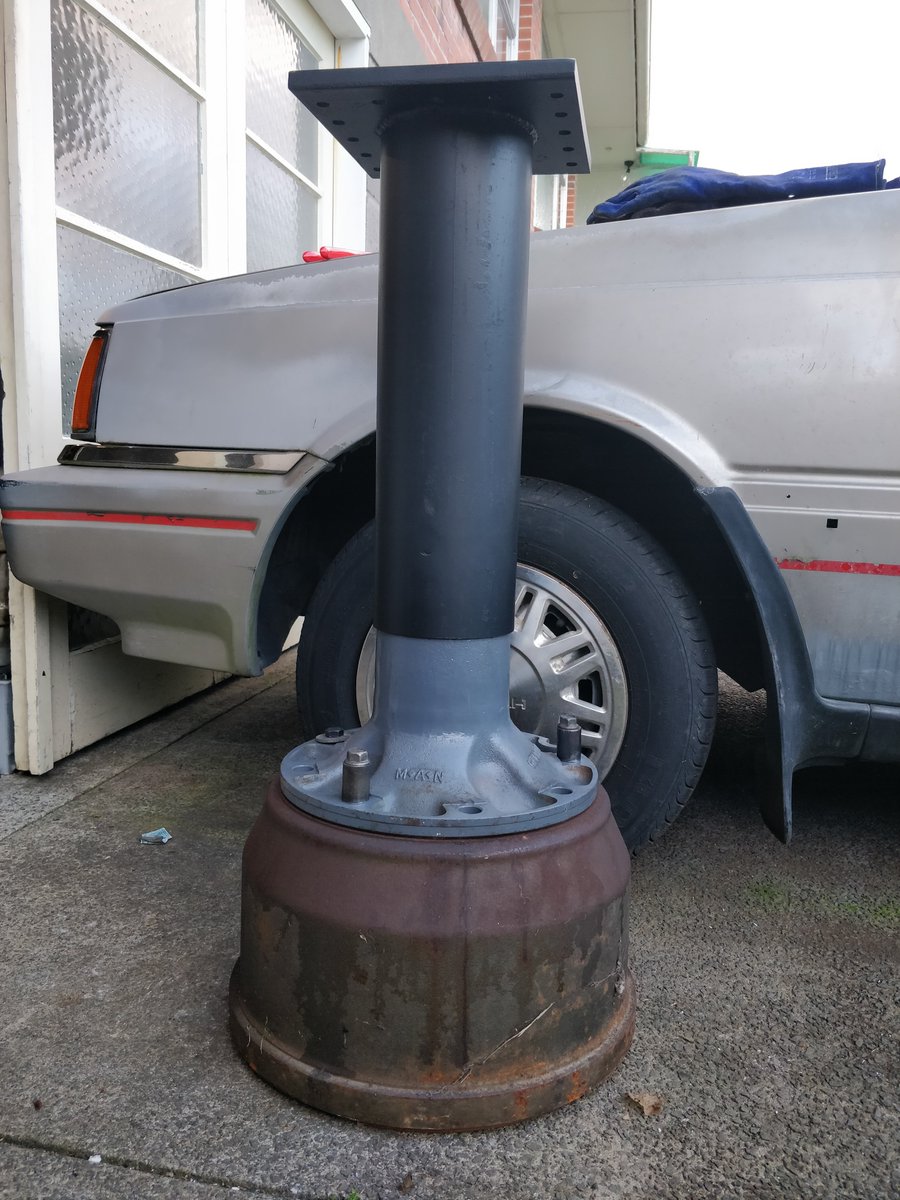



Today: https://twitter.com/FredCookeNZ/status/ ... 7364406272
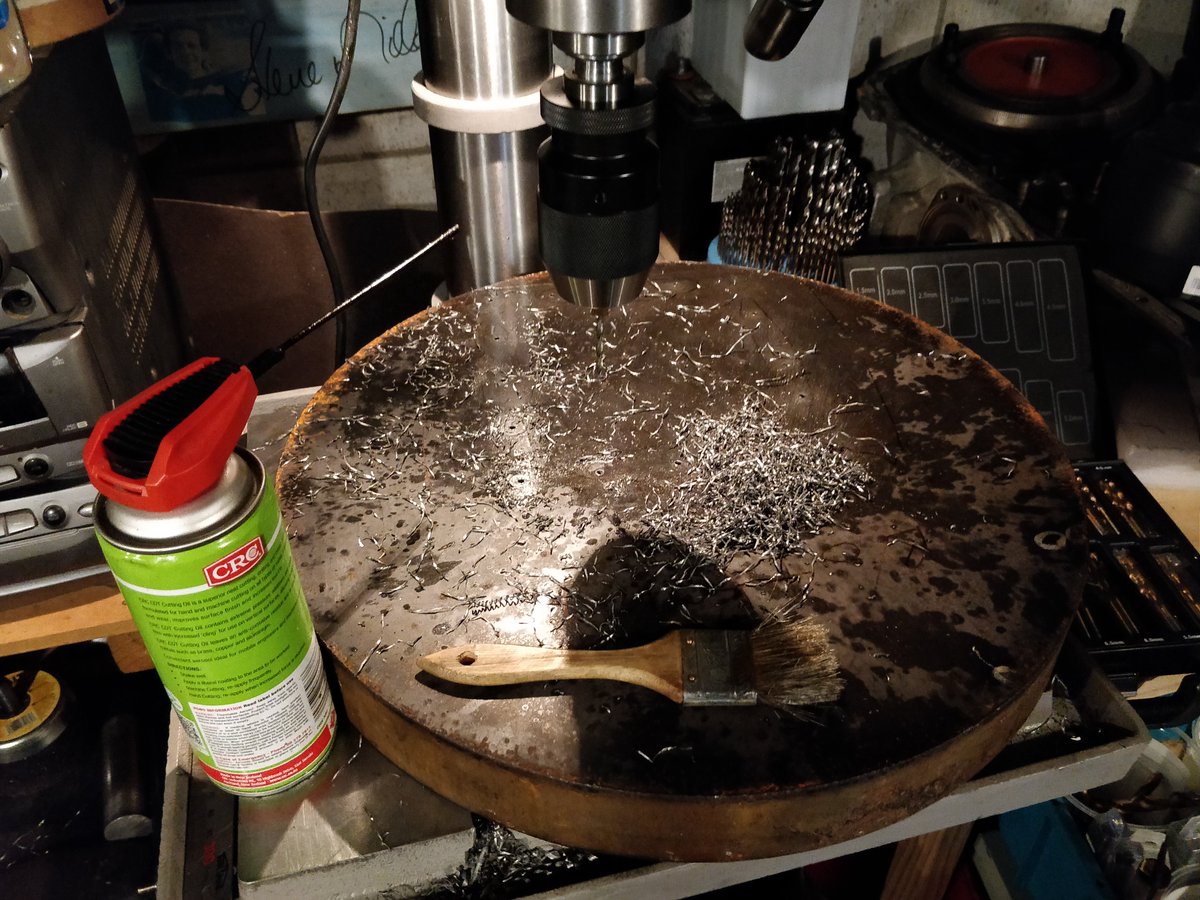
3 good deep quality plug welds and a shitty no-glove arm-inside-tube weld around the perimeter from only the top side. I intended to do a better one around the other side, but now that it's pressed together... no. :-D
Strong enough, if not pretty. I could add 3 more plug welds and then guarantee it'd be overkill strong, but I already tightened the fastener as much as I physically could and didn't come close to breaking what's already there.
Additional plan, going to splurge on 22kg of lead shot for duck shooting and fill the tube with it instead of sand. Will add stability, push the overall weight just past 200kg, and deaden any ringing from impacts. I hope.
Disk is drilled 40mm deep in matching pattern (3.5mm then 8.5mm) and M10x1.5 tap set ordered from a German company (Volkel with funny o) but probably not made in Germany sadly. Sold me on three stage taps that aren't just taper varied, but are actually partial cuts so the final bottoming tap actually takes a fine cut of its own all the way through. Will see how that works out relative to the conventional Sutton Aussie ones I intended to buy.
A couple of lame updates:
Yesterday or the day before: https://twitter.com/FredCookeNZ/status/ ... 4512784384
Today: https://twitter.com/FredCookeNZ/status/ ... 7364406272
DIYEFI.org - where Open Source means Open Source, and Free means Freedom
FreeEMS.org - the open source engine management system
FreeEMS dev diary and its comments thread and my turbo truck!
n00bs, do NOT PM or email tech questions! Use the forum!
The ever growing list of FreeEMS success stories!
FreeEMS.org - the open source engine management system
FreeEMS dev diary and its comments thread and my turbo truck!
n00bs, do NOT PM or email tech questions! Use the forum!
The ever growing list of FreeEMS success stories!
Re: Mobile vice and small anvil / welding table
Haha, that sounds like so much funFred wrote:and a shitty no-glove arm-inside-tube weld around the perimeter from only the top side.


Then it definitely won't come apart, ever.Fred wrote:didn't come close to breaking what's already there.
I too have some Völkel taps. Never had particular problems with em, nor found them sketchy looking. What makes you think they aren't made here? Maybe you received counterfeit?
Awesome anvil, really

Re: Mobile vice and small anvil / welding table
Before I buy, I research. They have manufacturing facilities around the world in 6 countries or something, both their own and "partner" and partner use Volkel owned machines. So I have some faith that wherever they're made it'll be good enough for me, but I prefer to support first world manufacture as opposed to first world profit only, if that makes sense. The normal ones I would otherwise have gotten are made in Australia which is fine by me. That company owns the old NZ company that still makes drill bits here, and the ones I own both new and ancient imperial from generations by-gone. However along with those two good product lines, they have Chinese shit in there, too, which makes me suspicious of their brand in general. Meh. The world is fucked.
Welding inside the tube was okay, no sunburn on the hand, but I couldn't see well, so the welds were not well aimed nor well directed/laid. Hence shitty. :-) The three 10mm plug welds were likely enough to hold back my power bar on the M14, so it's not going anywhere, no worries.
Anvil table. A table to rest some "ASO" railway iron on ;-) Once I have the scale acid stripped and the surface sanded/ground smooth I won't want to beat on it directly too much :-D
Welding inside the tube was okay, no sunburn on the hand, but I couldn't see well, so the welds were not well aimed nor well directed/laid. Hence shitty. :-) The three 10mm plug welds were likely enough to hold back my power bar on the M14, so it's not going anywhere, no worries.
Anvil table. A table to rest some "ASO" railway iron on ;-) Once I have the scale acid stripped and the surface sanded/ground smooth I won't want to beat on it directly too much :-D
DIYEFI.org - where Open Source means Open Source, and Free means Freedom
FreeEMS.org - the open source engine management system
FreeEMS dev diary and its comments thread and my turbo truck!
n00bs, do NOT PM or email tech questions! Use the forum!
The ever growing list of FreeEMS success stories!
FreeEMS.org - the open source engine management system
FreeEMS dev diary and its comments thread and my turbo truck!
n00bs, do NOT PM or email tech questions! Use the forum!
The ever growing list of FreeEMS success stories!
Re: Mobile vice and small anvil / welding table
So the tap set arrived the other day and it was indeed German made which was pleasing to me. Less expensive than the Australian ones and more innovative. Excellent.
Gave it a shot on one of the least important holes and got mixed results, but my fault, still, usable. Tried again last night and got good results, but hard work. Ordered a Starrett tap handle from a local company that had a better price than Amazon (and will order two more sizes and maybe the other type from them, too, after December 1st). Should arrive Monday or Tuesday and will make it a lot easier to do a nice job. Was using a 4 inch crescent adjustable spanner to do it, not easy to keep the pressure purely rotational torque.
Bought the fasteners to hold the braces to the flange and the flange to the table top and the vice plate to the braces. So I have enough parts/materials to see this through to near completion now.
Marked out the steel plate to design how I want the braces to be. Will re-mark from the other end back to front so I can do less cuts to get the parts I want/need.
Trimmed the flange so it doesn't stick out past the edge of the table top, too: https://twitter.com/FredCookeNZ/status/ ... 0224109570
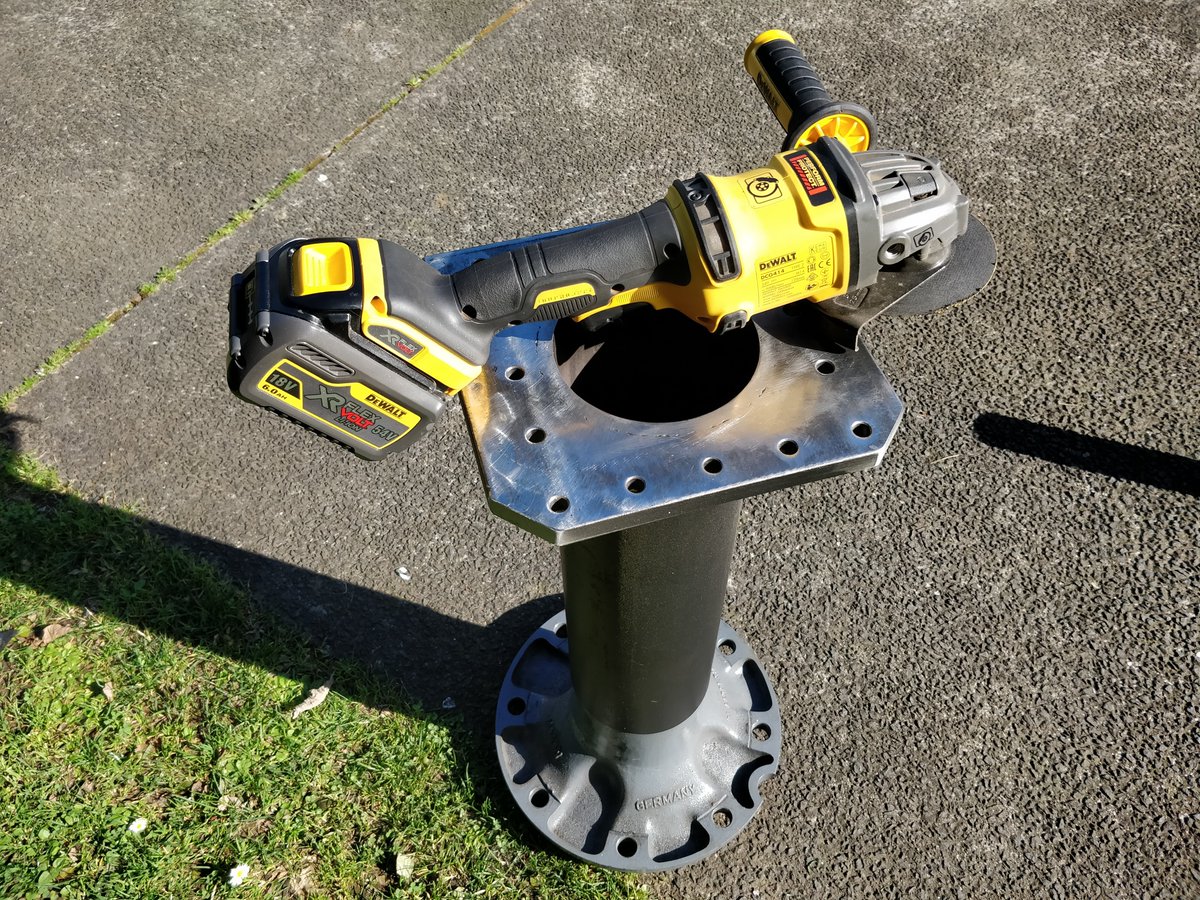

Cap screws laid out over the design: https://twitter.com/FredCookeNZ/status/ ... 0872560640

Chamfer to allow positive clamp on 6 direct clamps: https://twitter.com/FredCookeNZ/status/ ... 7854953473
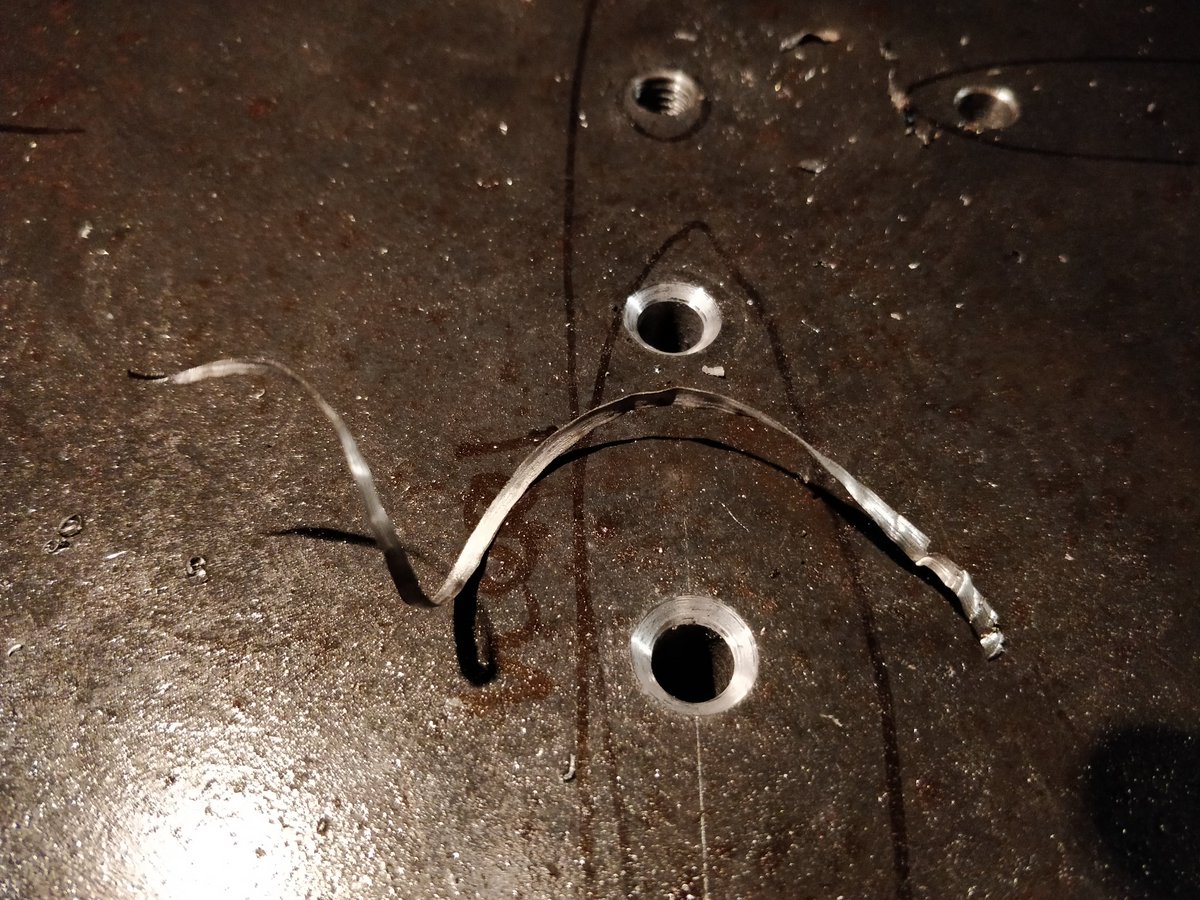
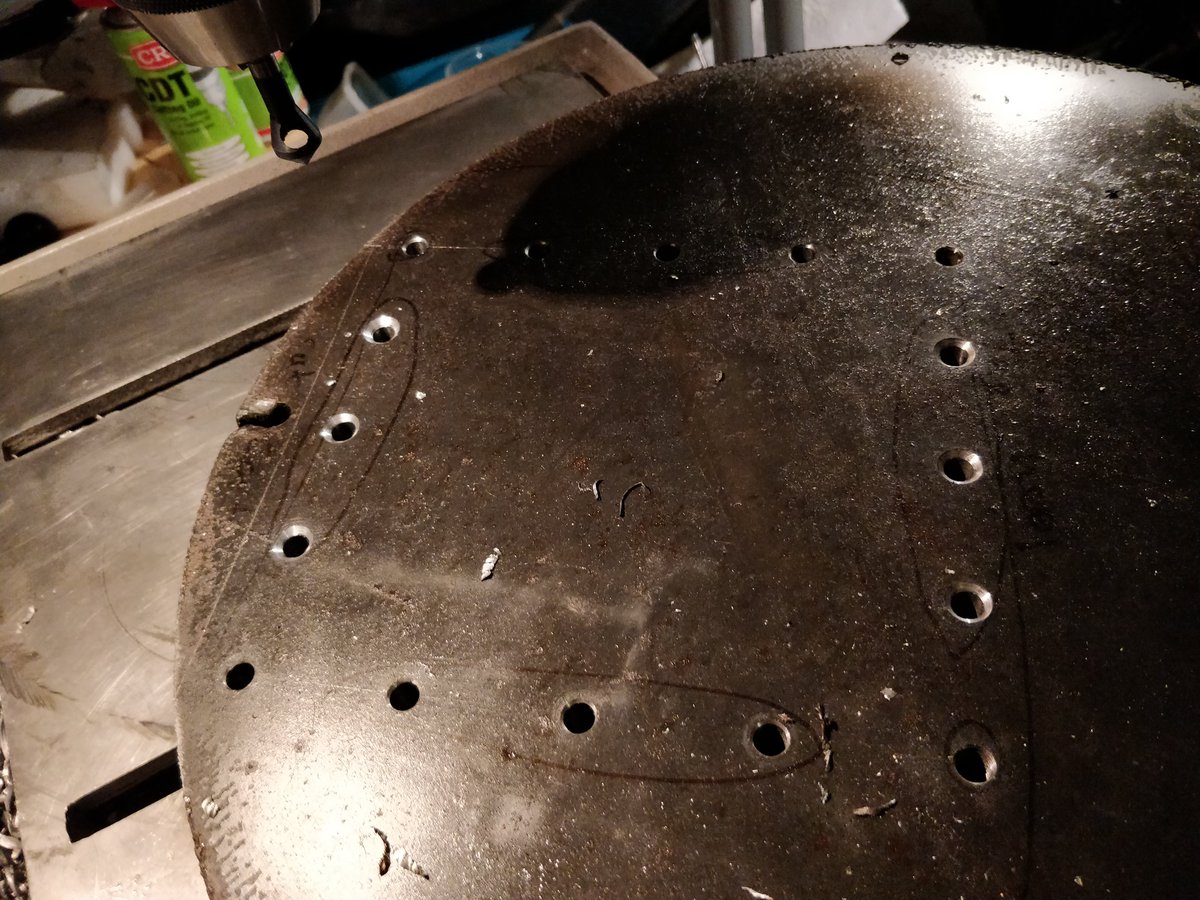
Taps with bolt showing 14mm gap bottomed out: https://twitter.com/FredCookeNZ/status/ ... 5779101696

Ordered cheap 16mm end mill to pocket drill with flat bottom: https://twitter.com/FredCookeNZ/status/ ... 2777646080

Grade 12.9 cap screws in 3 sizes and hardened washers: https://twitter.com/FredCookeNZ/status/ ... 7136755712

Marked out with vivid on the piece of steel in the wrong place just to design it: https://twitter.com/FredCookeNZ/status/ ... 3848517632


Taps and demo of hole after first attempt: https://twitter.com/FredCookeNZ/status/ ... 9614756864


Tap arrival, can see the different grinds on them: https://twitter.com/FredCookeNZ/status/ ... 2128287744
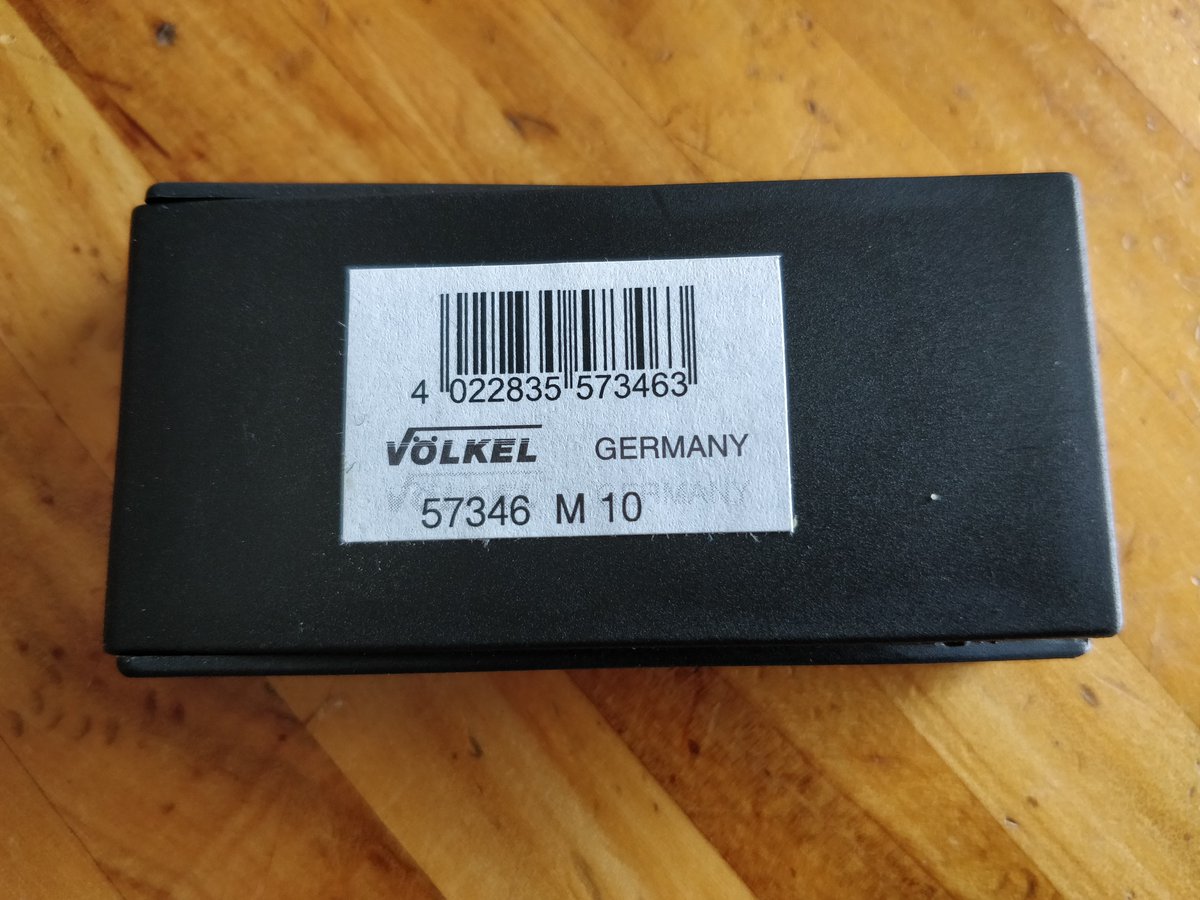

Marking out from flange with transfer punch, belonged in prior post: https://twitter.com/FredCookeNZ/status/ ... 7421074434

So in summary, waiting on the tap handle to continue, and cutting the big slab of steel up will have to wait till next weekend or one evening this week. New job starts Monday and doing heavy grinding in the evening isn't particularly socially acceptable. Plus have the Volvo 360 in pieces on the grass and need to wrap that up tomorrow before the weekend finishes and I'm out of sunshine time to repair it.
Gave it a shot on one of the least important holes and got mixed results, but my fault, still, usable. Tried again last night and got good results, but hard work. Ordered a Starrett tap handle from a local company that had a better price than Amazon (and will order two more sizes and maybe the other type from them, too, after December 1st). Should arrive Monday or Tuesday and will make it a lot easier to do a nice job. Was using a 4 inch crescent adjustable spanner to do it, not easy to keep the pressure purely rotational torque.
Bought the fasteners to hold the braces to the flange and the flange to the table top and the vice plate to the braces. So I have enough parts/materials to see this through to near completion now.
Marked out the steel plate to design how I want the braces to be. Will re-mark from the other end back to front so I can do less cuts to get the parts I want/need.
Trimmed the flange so it doesn't stick out past the edge of the table top, too: https://twitter.com/FredCookeNZ/status/ ... 0224109570
Cap screws laid out over the design: https://twitter.com/FredCookeNZ/status/ ... 0872560640
Chamfer to allow positive clamp on 6 direct clamps: https://twitter.com/FredCookeNZ/status/ ... 7854953473
Taps with bolt showing 14mm gap bottomed out: https://twitter.com/FredCookeNZ/status/ ... 5779101696
Ordered cheap 16mm end mill to pocket drill with flat bottom: https://twitter.com/FredCookeNZ/status/ ... 2777646080
Grade 12.9 cap screws in 3 sizes and hardened washers: https://twitter.com/FredCookeNZ/status/ ... 7136755712
Marked out with vivid on the piece of steel in the wrong place just to design it: https://twitter.com/FredCookeNZ/status/ ... 3848517632
Taps and demo of hole after first attempt: https://twitter.com/FredCookeNZ/status/ ... 9614756864
Tap arrival, can see the different grinds on them: https://twitter.com/FredCookeNZ/status/ ... 2128287744
Marking out from flange with transfer punch, belonged in prior post: https://twitter.com/FredCookeNZ/status/ ... 7421074434
So in summary, waiting on the tap handle to continue, and cutting the big slab of steel up will have to wait till next weekend or one evening this week. New job starts Monday and doing heavy grinding in the evening isn't particularly socially acceptable. Plus have the Volvo 360 in pieces on the grass and need to wrap that up tomorrow before the weekend finishes and I'm out of sunshine time to repair it.
DIYEFI.org - where Open Source means Open Source, and Free means Freedom
FreeEMS.org - the open source engine management system
FreeEMS dev diary and its comments thread and my turbo truck!
n00bs, do NOT PM or email tech questions! Use the forum!
The ever growing list of FreeEMS success stories!
FreeEMS.org - the open source engine management system
FreeEMS dev diary and its comments thread and my turbo truck!
n00bs, do NOT PM or email tech questions! Use the forum!
The ever growing list of FreeEMS success stories!