Okay, so the situation is as follows:
Tube squareness and hub detail:
https://twitter.com/FredCookeNZ/status/ ... 1761605632
Tube is square on fresh end, that can be the bottom. Slightly off on older cut end, that can be the top, and either shimmed prior to welding to the top flange, or ground till square first.
Bottom of the hub is not hollow like I had poorly / wrongly remembered, it has bearing stuff in there, and a nice obvious machined flat surface to put a disk over. If it was aligned perfectly, 102mm would be spot on, but given it likely won't be, and more weight down low = better, I'll make it oversize and maybe just square despite the round surface. If round 160mm would be max diameter before it fouled other surfaces.
I have a few things that can make this decision easier:
- 35mm ID seamless API tube, very strong (200mm piece available, 300mm piece in service elsewhere)
- 35mm bright engineering round bar (250mm available, need very little for original purpose)
- M14x2 tap, Australia made, quality, intermediate (not taper, not plug/bottoming)
- Knowledge that the "proof" load of an M14x2 12.9 fastener is 112kN or 11,000kg
- Knowledge that I don't need more than a few hundred kg of clamp force for this
- A drill press and an angle grinder and boundless enthusiasm :-D
Small tube and round bar:
https://twitter.com/FredCookeNZ/status/ ... 8575535104
So what I think I'll do is:
- Cut out the disk to go inside the tube, drill it for M14, space it up correctly, weld it fully around the lower side, drill and plug weld around the edge in 3-8 places
- Find some sort of rubber or plastic press in bung/cap for the top, size a hole in the top flange to suit that and ensure I can get my hand through to start the bolt
- Weld on the top flange with as much preheat as possible to reduce cupping of the flange, made of ideally 16mm plate but 12mm may have to do, same for 2 disks
- Sit tube upside down and rest small tube on welded in plate through hole in bottom of hub, measure and mark tube for cutting, cut say 5mm shy of the bearing surface
- Cut two pieces of 35mm bar stock in the 35-60mm range, drill to 12mm, centrally, maybe on a lathe, tap to M14x2, bevel heavily on one end
- Bevel the inside edge of both ends of the tube to match
- Weld in fully around the end, then through several holes around the sides
- Buy two more M14x2 cap screws and hardened washers
- Buy or scavenge a strip of 1.5mm sheet steel or even aluminium, maybe 11-25mm long (plate to end distance, minus weld height)
- Buy M20 (or smaller if cost prohibitive) cap screws and hardened washers and nuts for around the hub to drum interface
- Buy or scavenge some 1mm sheet to wrap around 4 of the M20 fasteners (or thicker if thread smaller) to get the hub centred on the drum
Then it's back to the top and the paint scheme!
Colours? Have black and white, could mix grey, or buy any other colour.
- Drum?
- Hub?
- Tube?
- 50mm table sides?
Not sure what will emphasis the nice blue vice on top best :-D Table top will be bright oiled or waxed steel. Will be etching the mill scale off with hydrochloric acid and rubbing with stones and oil until pretty. Cap screws likely to be black with gold passivated zinc hardened washers, but not sure yet.
Best photochop job of the below photo wins a thank you :-D
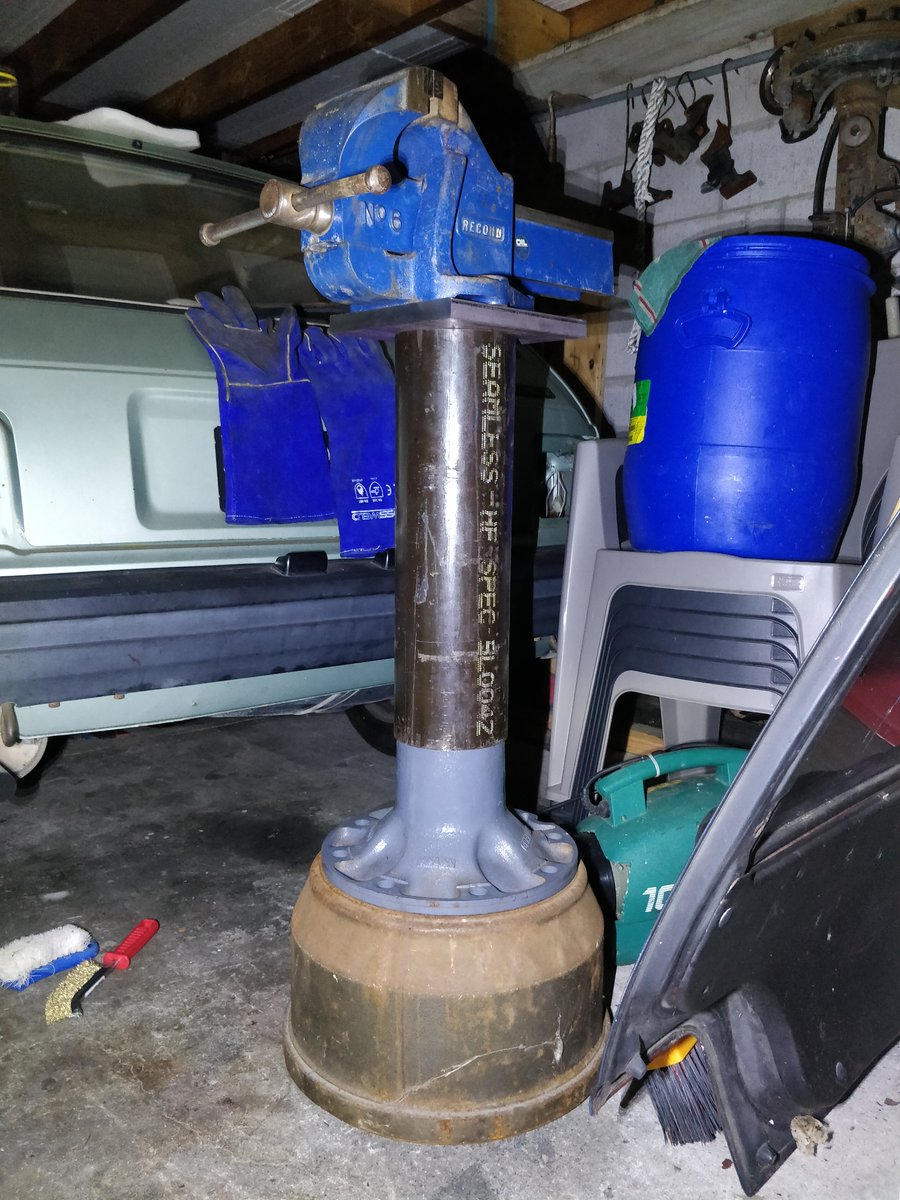